The Vattenfall Solar Team has been taking advantage of the ParaPy platform to design the optimal aerodynamic shape for their solar cars since the Nuna9 in 2017. We interviewed Max van der Waals, Aerodynamics Engineer for the latest solar car NunaX, about the impact the ParaPy platform has had on their design process.
What is so challenging about designing a new Nuna car every year?
Every other year the Bridgestone World Solar Challenge is held in Australia. Before each team starts their year, the new regulations are released on world environment day. These regulations have a major impact on the design of the team’s solar car. For example, several constraints are set on the design space, such as restrictions on the vehicle’s dimension. Each team is challenged by finding the optimal solar car design within this design space. As aerodynamic engineers, this means that after a certain concept has been chosen by the team, they are left with the challenge of finding the shape for this concept which produces the least amount of drag to reduce the air resistance of Nuna.
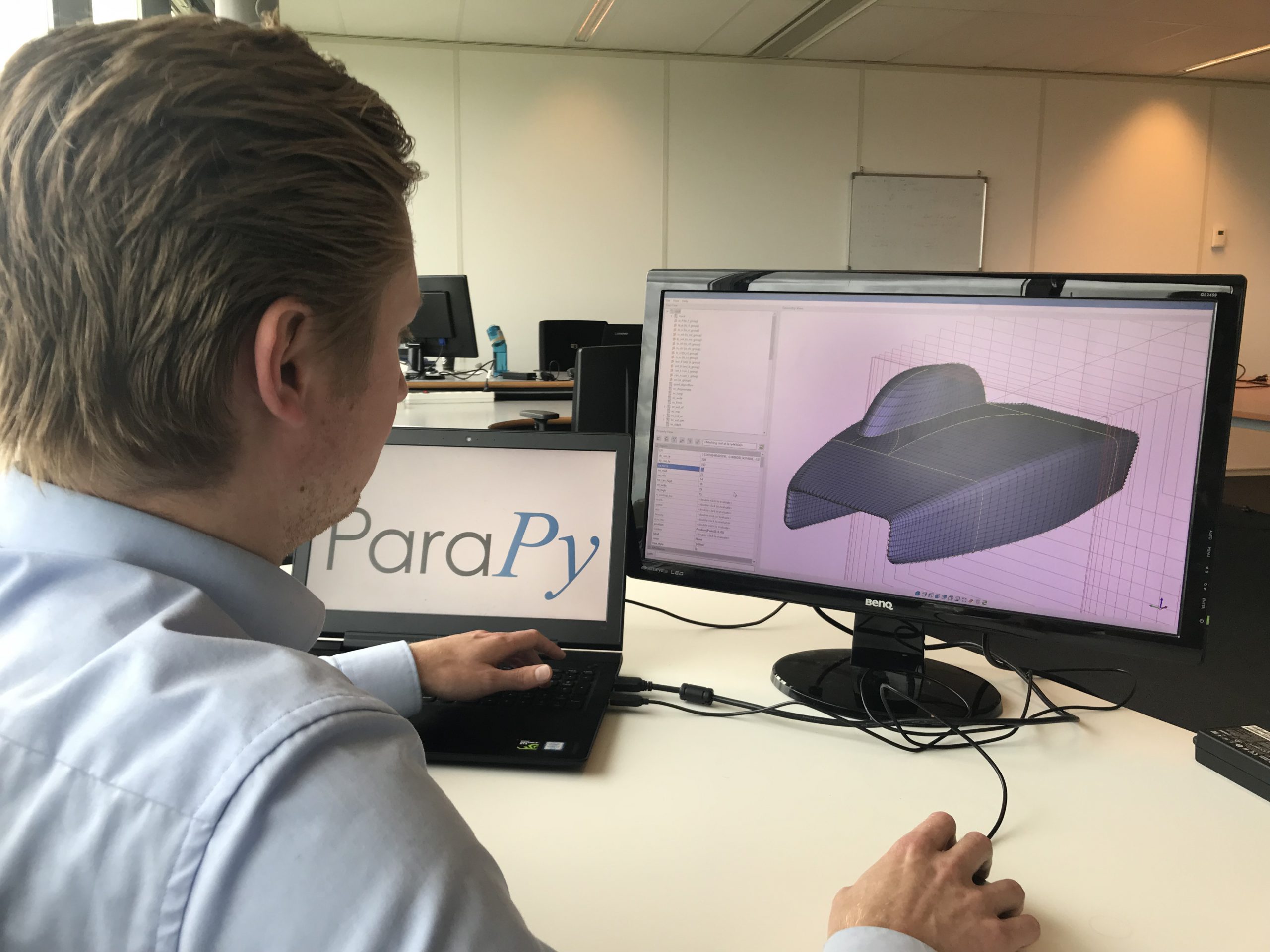
Since the complete body of Nuna has to be designed in several months, the team is limited in the amount of research and optimization that can be performed. Each reliable iteration could potentially increase the performance of Nuna and any additional iteration that can be done is therefore very valuable to the team.
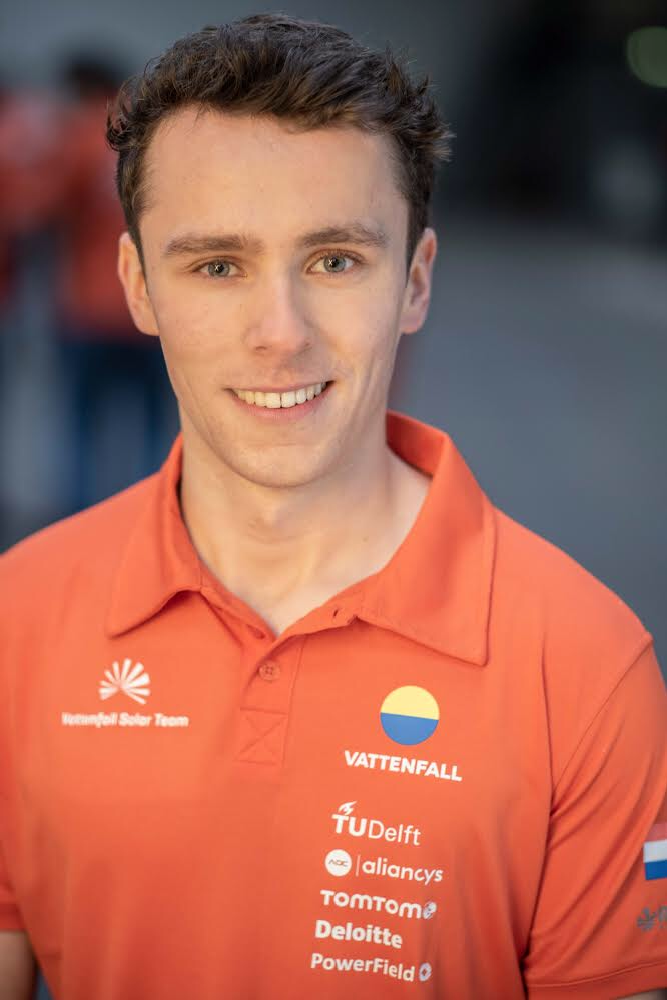
What is so challenging about the aerodynamic design of Nuna?
Aerodynamically speaking, Nuna operates at relatively low velocities around 100 km/h. This means that any aerodynamic improvements will be very sensitive to small changes in the design of the car, which sometimes makes it very difficult to design by hand. Although it is possible to improve the design with manual adjustments, it remains a big challenge to find the global optimum considering the large number of systems that have to be integrated within margins of only a few millimeters. For example, the front suspension and wheels have to fit in the wheel covers of Nuna while being able to reach their maximum steering angles. As you can imagine, with all these types of physical limitations, it becomes a major challenge to find the optimal aerodynamic shape. In the end, the aerodynamic design is about the challenge of finding the optimal shape that can house all the car’s systems.
How was the aerodynamic design of the car performed before ParaPy?
Before the use of ParaPy in our design process, the aerodynamic optimization was relying more heavily on computational fluid dynamics (CFD). This meant that each iteration took much longer. Additionally, in the past, several wind tunnel test have been performed. Especially for the more complex flow interactions the use of experimental simulations provided reliable data. However, since the quality of numerical simulations has increased it has been possible for us to depend more heavily on computer simulations.
How much time did it take to do a single aerodynamic design iteration?
A single iteration could take more than a full day to complete. Since the aerodynamic design is so dependent on the available space required by the other systems in Nuna, it was a very intense job iterating on the design by hand and finding the numerical solution afterward.
What was limiting you in doing more design iterations?
How does your Nuna aerodynamic design app work?
Using ParaPy it has been possible to implement all of the mechanical, structural, and electrical systems as design constraints for a given aerodynamic shape. Based on the extensive geometry library in ParaPy’s modeling toolbox, we can model the body and internal systems of Nuna in a systematic matter. After the aerodynamic shape is modeled, we take advantage of ParaPy’s simulation toolbox to mesh the shape and run the aerodynamic analysis with a 3D panel method. That analysis provides us the aerodynamic flow around the car and the number that is of key interest to us: the drag.
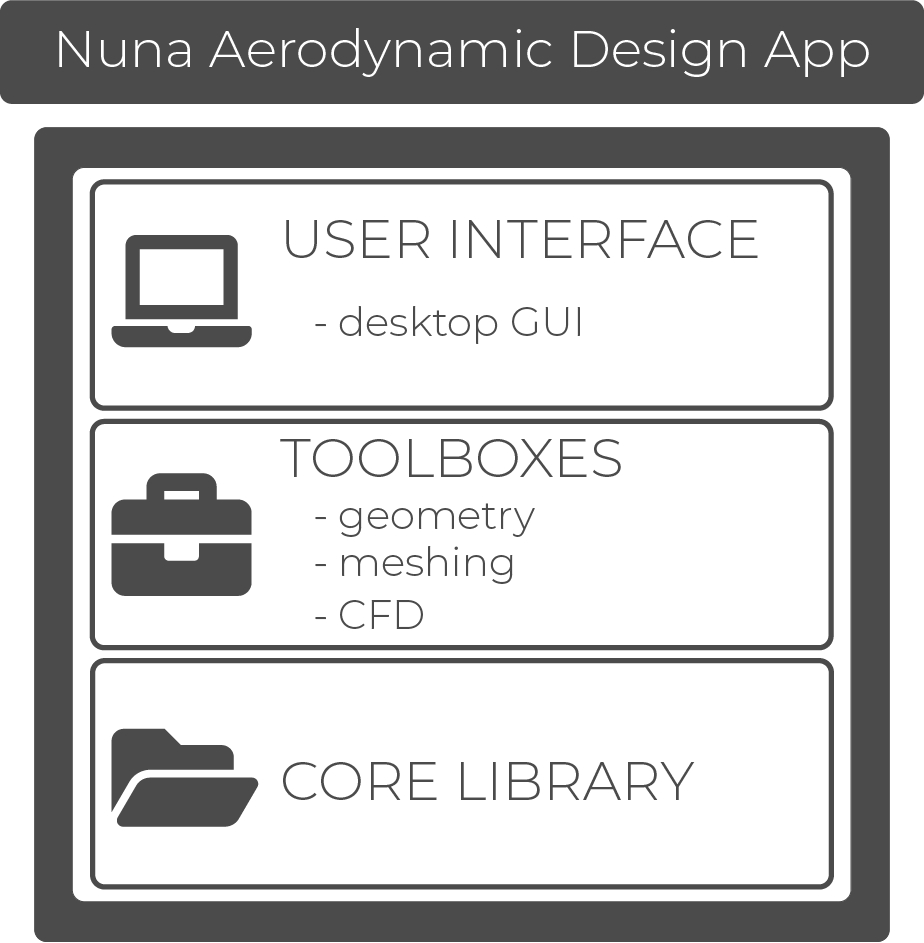
How have you experienced working with the ParaPy software package to create your design application?
Working with the ParaPy platform has been a great experience, as it is very intuitive to implement. The versatility of the platform has allowed us to quickly develop an application that can be implemented in our design process. Already in the first year of using ParaPy, the team was able to base their design on results produced by the application. During our year, the team was able to improve the efficiency of the application’s implementation in our design process and to increase the level of complexity by moving towards a more automated design process.
How long did it take to build the app?
The app was built in a relatively short time. The ParaPy platform provides a clear basis allowing an easy implementation in the design process. It took only around 2 months to build the app. As the ParaPy language is easy to learn, each new Nuna team will be able to add new capabilities and features to the design application that they inherit from their predecessors.
How are you using the app?
In our team, we work with three team members on the aerodynamic design. This means that all of us were involved in the development of the app as well. Using ParaPy and the constraints that are defined by us, we let an optimization algorithm decide what direction the geometry shows the most potential. In the future, we think it is possible to implement more automation and have ParaPy assist in the detailing of the design.
Our optimization takes into account several design constraints. Based on our experiences and simulations we let ParaPy design several thousands of analysis-ready models with each one being evaluated on its performance. This leads to a large reduction in drag and therefore a faster solar car.
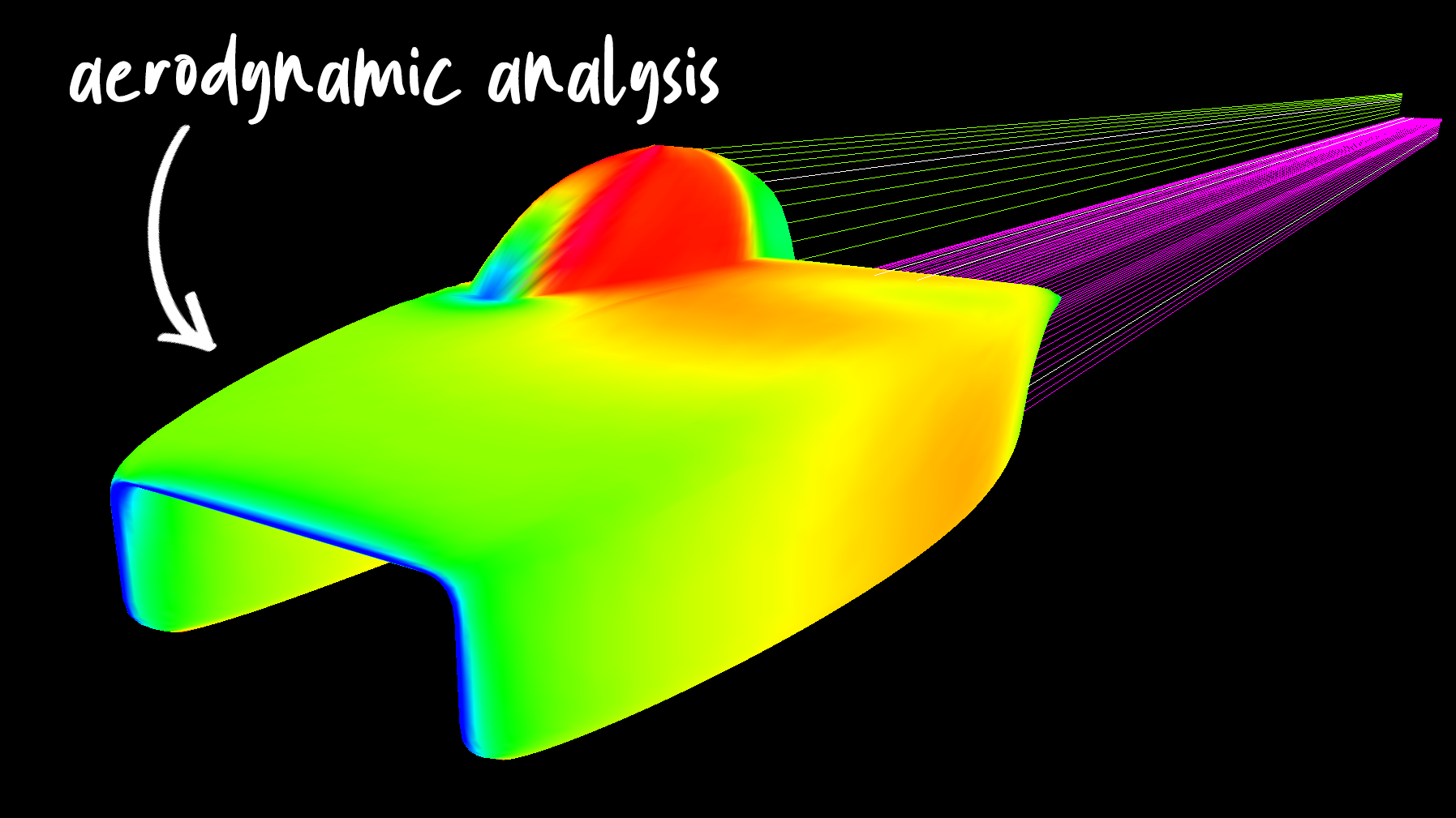
What has impressed you most about ParaPy in your design application project?
What has impressed us the most is the efficiency ParaPy provides in our design process. Normally it is very difficult to build a multi-disciplinary design optimization. However, with ParaPy we have found a great balance between accuracy and efficiency allowing us to rapidly iterate on aerodynamics.
ParaPy allows us to evaluate the aerodynamic performance of thousands of design iterations in just a few hours. Compared to a conventional design process this is a completely different level of efficiency and that helped us tremendously to find the most efficient solar car.
Were you able to find new solutions that went against engineering intuition?
Our ParaPy application has indeed found interesting solutions that we did not think of beforehand and therefore basically expanded our feasible design space. The combination of the many systems that have to be integrated and the small margins available to obtain a valid solution make it near to impossible to find the same optimal shape by hand. Thanks to ParaPy, we have been able to perform so many iterations that new interesting designs were found that further improve the performance of Nuna.
What has been the impact of using the app over the past three years?
With the introduction of ParaPy into our design process, we have been able to further develop the aerodynamic design of Nuna and make her more competitive. With the increasing complexity of all the systems that are found in a solar car, we have noticed the importance and success of a reliable and efficient design optimization tool to make our solar car aerodynamically efficient and stable like never before.